If Supply Chains Could Speak
The importance of Industry 4.0 and Operational Transformation
The current global crisis is causing people to rethink their supply chains, operations, and organizational adaptability. Industry 4.0 and specifically Connected Manufacturing will now be more important than ever as companies wrestle with these issues. This is the second in a series of discussions between CGS Fellows, Angie Tuglus and Pat Hillberg on these topics.
_____________________________________________________________________________
Tuglus: As organizations think about a new future, it is time to take a serious look at control, capability, and adaptability. In our last blog conversation we discussed how increasing stockpiles will not solve the real underlying issues. There is a serious deficiency in organizational adaptability, and organizations must rethink their dependencies, span of control and ability to adapt.
Around the globe, businesses are realizing they do not know, or control, their supply chains and operations as well as they thought.
Hillberg: Right. Supply chains have become complex and distributed, and will be impacted for years to come (How the pandemic disrupts global value chains).
Think of the coordination needed… the components in a car assembled in the US originate from many countries: Canada, Mexico, Japan, China, India, Germany, … If any one of these regions is in an extended lock-down, the ripple effect impacts everyone throughout the chain. If the factory in the US cannot get engine components from China, then it will cancel the radios set to be delivered from Germany.
Tuglus: Recently, people everywhere have turned, looked intently at their supply chain, and asked “what were you thinking?” They are going into the back office, shining a bright light on their operations, and interrogating them: “what were you doing, supply chain, on the night that the pandemic halted production and our ability to operate?”
And the supply chain replied: “Doing exactly what you set me up to do. Running an intricate global network, to yield the lowest cost possible, while meeting speed and quality specifications. It’s not my fault!”
Hillberg: If supply chains could talk…
Tuglus: Exactly. We need to enable that. I want supply chains and operations to speak to us.
Hillberg: Are you talking about robots again? We both love robots.
Tuglus: No. Though…tempting, very tempting. No. We’ll save that for another day. I’m talking about better monitoring, sensing, and alerts. We need better visibility such that the interrogation process becomes unnecessary. Where our supply chains and operations can easily communicate information. Ultimately, this will provide greater adaptability and control. Greater capability to rapidly adjust to large market changes, regardless of how those changes are initiated – competitor, regulation, political unrest, climate crisis, global health crisis, etc.
Your automotive example showcases this. Each first-tier supplier to an OEM has second-tier suppliers, who have 3rd-tier suppliers, etc., and the OEM has little visibility beyond the first tier. As purchasers look across the world-wide pandemic landscape, they do not have the visibility to know if promised supplies will be delivered. In an increasingly Connected World, this feels oddly like a black box.
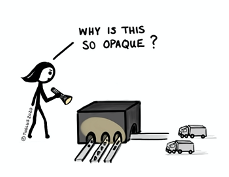
Hillberg: There are prominent failures in which increased visibility could have had a material impact. For example, in 2014 General Motors executives recognized that some ignition switches included a sub-standard spring, which would allow the switch to fall out of the “Run” position while the car was moving, and in the process disable the airbags immediately before a crash. More than 100 people died for lack of an operable airbag. GM had no visibility as to which automobiles might use the sub-standard switch (about 20% did) so they needed to recall ten-year’s worth of vehicles.
Tuglus: That is tragic for those who died. Also, nerve-wracking and inconvenient for the 80% who had their vehicles recalled, but did not know they had standard switches and were therefore safe. And, obviously, it was rather damaging to the brand. Are there other examples?
Hillberg: There are recurring issues of safety in the food supply. In 2018, at least 200 people became ill, and 5 died, due to E. Coli poisoning linked to romaine lettuce. The outbreak occurred in late April, which is about the time that the romaine supply chain shifts from Yuma, AZ to Salinas, CA, 500 miles away. The FDA theorizes that the romaine grown in Yuma picked up bacteria from a cattle feed lot which was upstream, but the packaging didn’t indicate the source of the lettuce; the great majority of the discarded romaine was from Salinas and never close to the infected stream.
Tuglus: So huge amounts of lettuce were thrown away unnecessarily. That is very sad. Unless, I suppose, if you are a salad hater. It seems difficult to comprehend this waste, as technology is now available to increase our visibility into these operations. With the new sensors and connected devices, so many things are possible. All these things are playing into Industry 4.0. What are exciting things you see happening to increase operational visibility?
Hillberg: Let’s talk about Digital Twins and Threads. The concept of a Twin is that we maintain all the information about a physical object in the virtual world, so that we don’t need access to the physical object to gain information about it. (The concept originated with NASA… it is really hard to measure things once the spaceship is in orbit.) The Thread is the mechanism by which we keep virtual and physical instances synchronized, so that no matter what happens to the physical, the virtual continues to reflect reality. In other words, there is a virtual Twin for every physical thing, and a Thread which allows us to look at the virtual and know it reflects the physical.
So, imagine having Digital Twins/Threads of the factories which manufacture components which are assembled into a car or plane, or whatever else. Component factories are all over the world, and I imagine a push to localize supply chains. We want to build components near to where they are consumed and want to share information about their manufacture world-wide. This could even have major impact on how we measure world trade; we don’t need to trade physical items we can instead trade information about how to manufacture them. The World Economic Forum refers to these as Lighthouse Factories.
Tuglus: So, I imagine putting on my virtual reality headset, and entering a room with my colleagues across the world. In front of us sits a three- dimensional factory. We can open up the factory to peer inside, or light up all the electrical work, or see all the operating statistics of a machine or a production line. And follow the supply of materials out of the factory to see where everything is coming from, and key pieces of information at each stop. That’s great. Now if I can fold my VR headset into a pocket, I have a pocket factory I can take anywhere.
Hillberg: or you could look at it on your phone. Check out this video on YouTube.
Tuglus: Nice. Really, as long as we can get visibility into operations in a way that is easy to understand and connected for automatic update, then we are in a good place. Done well, measurements and other data can be captured at critical points, and alerts be set up for operators. Then the supply chain can speak to us.
Hillberg: But as cool as new technology is, our corporate processes are built around what already exists. New technology allows for new processes, but cultures are tied to the status quo, and it is hard to learn new things.
Tuglus: Now we’re getting into organizational transformation, one of my favorite topics. Concept to reality. First, they need to understand what is possible. That’s where visibility comes in. This is the kind of information you love to bring to your class, right?
Hillberg: Absolutely. In addition to technical concepts like Twins and Threads we look at cultural resistance to change.
Tuglus: And that’s where the complexity comes in. Figuring out how you should harness disruption, given your organizational goals and current state, well, that’s the easier part. The challenge comes when you begin to take into account the people system and set out to transform it in a way that actually gains the business value you desire. This is the real reason so many operations are still opaque.
We don’t have time now to go deep into the transformation process, but suffice it to say, there are some secrets to driving organizational change while avoiding pitfalls and navigating corporate dysfunction. To begin, though, start by gaining an understanding of the possibilities of disruption and your current state. And begin to imagine how to make your operations speak to you.
If you would like to explore how you can deploy Industry 4.0 concepts to transform your operations, please reach to us at info@cgsadvisors.com.
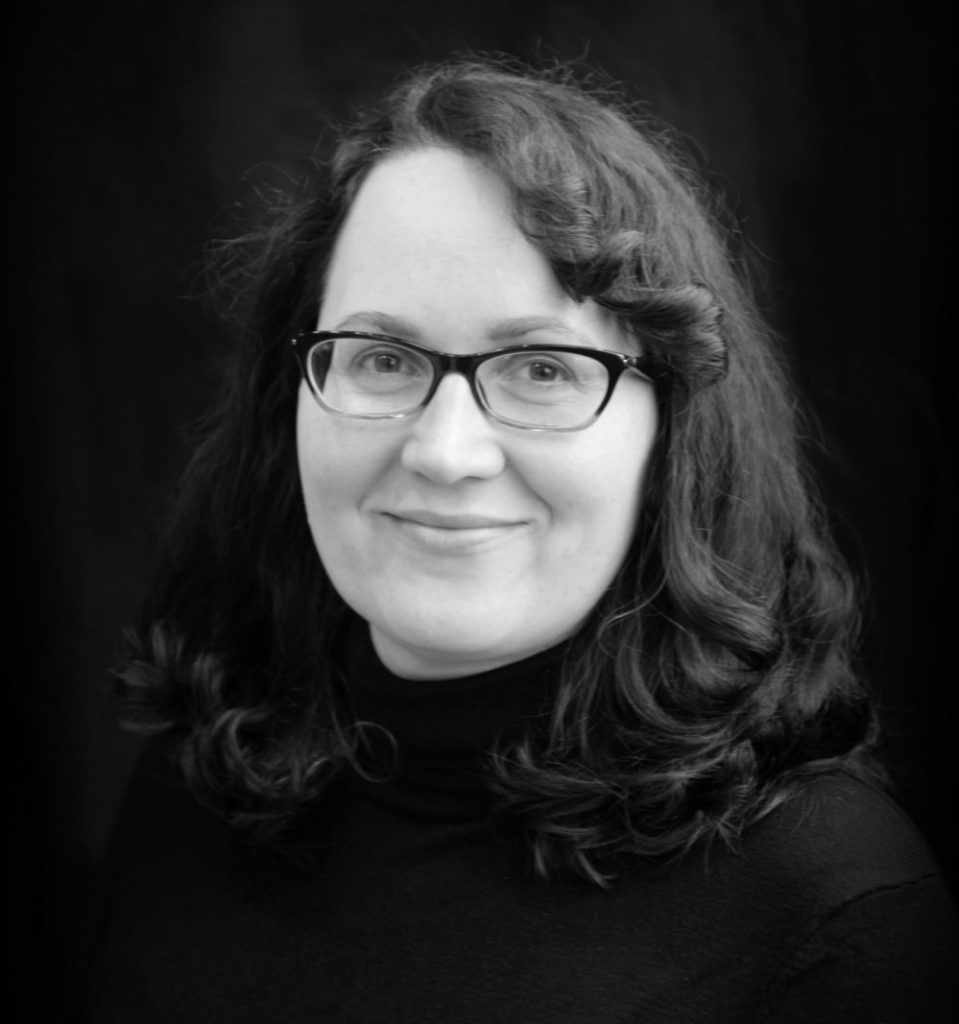
CGS Fellow Angie Tuglus is an expert in operational business transformation and innovation, from startup to Fortune 10. A former executive in both technology and operations, she holds an MBA, a BS in Engineering, and likes to explore the business implications of trends, events, and technology.
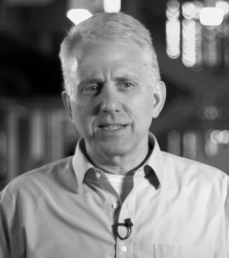
CGS Fellow Patrick Hillberg, PhD is an expert at Product Life Cycles, Industry 4.0 and Workforce Development. He has a Ph.D. in Systems Engineering and teaches a graduate course in engineering management at Oakland University. He likes to look at the events which happen around us and think about how they fit into larger systems.