If Only We Had a Stockpile of Ventilators
Rethinking supply chains, operations, and organizational adaptability with Angie Tuglus and Patrick Hillberg, PhD
The current global crisis is causing people to rethink their supply chains, operations, and organizational adaptability. This is the first in a series of discussions between CGS Fellows Angie Tuglus and Patrick Hillberg where they assess the world and predict the future.
_____________________________________________________________________________
Tuglus: As organizations emerge from crisis management mode, it is time to take a serious look at control, competency, and adaptability. Let’s talk about stockpiling today. There has been a lot of chatter about stockpiles lately.
Hillberg: The thought is that we should have had a much larger supply of medical equipment on hand to deal with a respiratory-based pandemic, but the reality is more complicated. Specialized medical devices like ventilators are expensive to produce and require maintenance if left in long-term storage: batteries go bad, hoses become brittle, and devices must be maintained to ensure they are ready to be deployed on short notice. Let’s be clear, increasing the domestic production capacity of ventilators to support the COVID-19 crisis response brought great social value. And in many cases, ventilators saved lives, but they aren’t a silver bullet.
Tuglus: So even if we had stockpiles, we cannot simply stick the equipment in a room and forget about it until we need it. But stockpiling can’t be the only option. I’m sure there are more possibilities.
Hillberg: Exactly, and that is the stockpiling conundrum – the cost, the storage, the making sure the equipment doesn’t disintegrate or decrease in efficacy over time.
Tuglus: I think stockpiling and reserves are a surface level discussion, masking an underlying issue. It is not feasible to guess at what needs to be stockpiled. It is about adaptability. It is about needing flexible capabilities and innovative thinking, so we can rapidly shift and retool to produce what we need at the time it is needed.
Hillberg: Explain further. You like to make things real for people. Give me an example.
Tuglus: For instance, recently a number of companies, in a variety of industries, have been able to rapidly retool their manufacturing to make face shields. Let’s take a moment to consider just how diverse these companies are: a wood products company (Woodchuck), a bike helmet company (WaveCel), and a film prop company (Hero Solutions). Just to name a few.
With equipment like 3-D printers and laser cutters, combined with an innovation mindset, they were able to rapidly prototype in days and manufacture within a week or two. Even some schools have been using their 3-D printers to make face shields. And, of course, thousands of people and social organizations have been making cotton masks. But most industries are not that nimble. Not in capability nor in mindset.
Hillberg: Companies used to own more capabilities, more of their supply chain. They kept their suppliers close, even to the point of rotating employees between companies. Over time, companies moved into a more complex and fragmented supply chain in pursuit of lowest cost across the globe.
Let’s look at automobiles: 20,000 parts, sourced from all over the world. If 19,000 parts are available, but 1,000 parts come from a region under shutdown (for whatever reason – pandemic, political unrest, environmental crisis), the automaker cannot build cars. After a week or two, everything comes to a halt. A $30,000 automobile might be held up for lack of 10-cent resistors.
Tuglus: Over time, many organizations have built an intense focus on outsourcing as much as you can and on keeping only a very few “core competencies” in house. And their suppliers are also outsourcing. As are their suppliers. Suddenly you have 3 corporate bureaucracies to mobilize in order to adapt. Or more. Very few organizations are designed with rapid adaptation in mind.
Hillberg: You’re right. We’re dependent on a multi-tiered, global, and opaque supply chain which is fragile at every step. We saw this a few years ago in the wake of the tsunami which struck the reactor at the Fukushima Daiichi Nuclear Power Plant in Japan; suddenly it was very difficult to get parts from that region.
And there a number of famous examples where companies took outsourcing too far. For example, when Dell outsourced too much of their core competency to Asus. Dell purchased component circuitry from Asus, then outsourced motherboards, product design, and eventually everything except the Dell brand. Asus ultimately was strong enough to sell computers on its own, under its own brand.
Tuglus: Companies should definitely be re-assessing what needs to be under their control and making some changes. In some cases, redefining what is considered core. It’s time to reimagine operational control and core competency from the lens of organizational adaptability.
Hillberg: We will need to localize core competencies. We have supply chains built around the concept of lowest cost, without recognizing the unintended cost of pandemic disease and invasive predators. We need to increase the level of societal value without also increasing global temperatures. We need to communicate information about our products without having to ship their physical masses around the world.
Let’s talk about what you mean by organizational adaptability.
Tuglus: So here is how I imagine it. You know the old adage about teaching a person to fish versus giving a person a fish?
Hillberg: Yes.
Tuglus: The world has become great at building fishing rods. But what happens when suddenly, for whatever reason, people are no longer fishing? Or you are not allowed to sell fishing rods? How quickly can you adapt to provide something else that people need, such as another way to acquire food? Can your rods and fishing line be fashioned into snares to catch rabbits? Do you have the control, capability, and ecosystem relationships to adapt and try things fast? Would you even think of it?
Most established organizations have not only outsourced much of their control, they also lack the organizational capability and mindset for rapid testing and action.
Hillberg: Speed of response is certainly critical. That is what almost bankrupted Prestige Ameritech, a mask maker, a few years ago when the H1N1 influenza virus was reaching epidemic levels. They spent millions of dollars building new manufacturing capabilities, hired 150 workers, and then the flu crisis suddenly ended. The company nearly went bankrupt.
Tuglus: Right! You can’t be building up your whole factory from scratch. You need to be able to transform what you have and what you can control. As ventilators grew scarce, medical staff found other solutions to help patients breathe, including modified CPAP machines and even birthing beds. We need to see this type of ingenuity happen fast and at larger scale.
We need to be innovating, rethinking our capabilities – both inside our organizations and with partners. And rapidly collaborating to transform our ecosystem. You can have supply chain partners, but those relationships must have adaptability. Purely contractual “lowest cost” relationships are not going to cut it.
Hillberg: What do we think about the Mayor of NYC’s plan to build a 90-day stockpile of masks, gowns, face shields, and other safety gear?
Tuglus: Look, some amount of supply is good. Organizations everywhere should certainly be re-evaluating their just-in-time, on-demand operations, and the trade-offs. They should ask: where have supplies been allowed to drop to extremely risky levels in favor of reduced carrying costs? But that is just one piece of the puzzle.
Addressing this does not solve the real underlying issues. It just buys more time. This situation is bigger than stockpiling. There is a serious deficiency in organizational adaptability. Organizations must rethink their dependencies, span of control, and ability to adapt.
Hillberg: Ultimately, we need to localize the supply chain and reduce systemic risks.
Tuglus: And increase adaptability. Stockpiles are not the answers
Hillberg: Agreed.
Tuglus: It occurs to me that in order to do this, organizations will need better visibility into their operations.
Hillberg: Absolutely. Let’s talk about that next time.
Tuglus: Looking forward to it.
For more information on how CGS Advisors can support your organization increase its adaptability, email info@cgsadvisors.com.
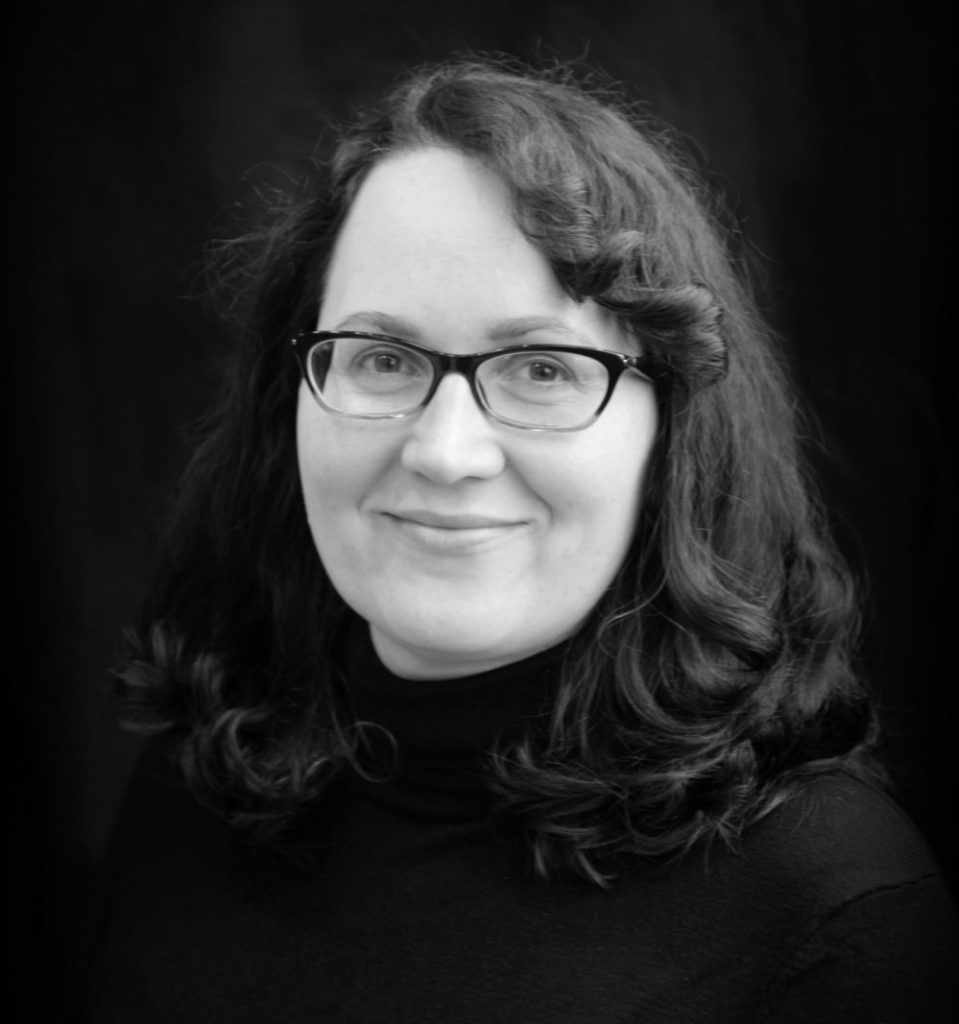
CGS Fellow Angie Tuglus is an expert at Transformation of Operations – successfully delivering large, cross-functional change initiatives, from concept creation through to delivery. Angie brings experience from her years in Chief Operating and Innovation roles to CGS clients, from startup to Fortune 10. Angie holds an MBA, a BS in Engineering, and likes to explore the business implications of trends, events, and technology. Angie also writes on a wide array of topics on her personal blog.
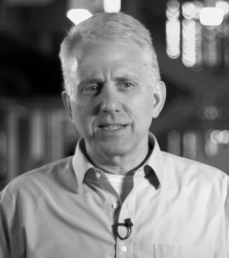
CGS Fellow Patrick Hillberg, PhD has over 30 years of industrial experience. Pat is an expert in the fields of Product Lifecycle Management (PLM), Industry 4.0, Workforce Development, and Robotics and Machine Vision Applications. Patrick’s experience spans a variety of industries and has allowed him to engage with developers, users, and leaders in the C-Suite of organizations. Pat has a PhD in Systems Engineering and likes to look at the events which happen around us and think about how they fit into a larger system.